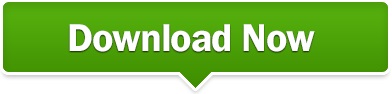
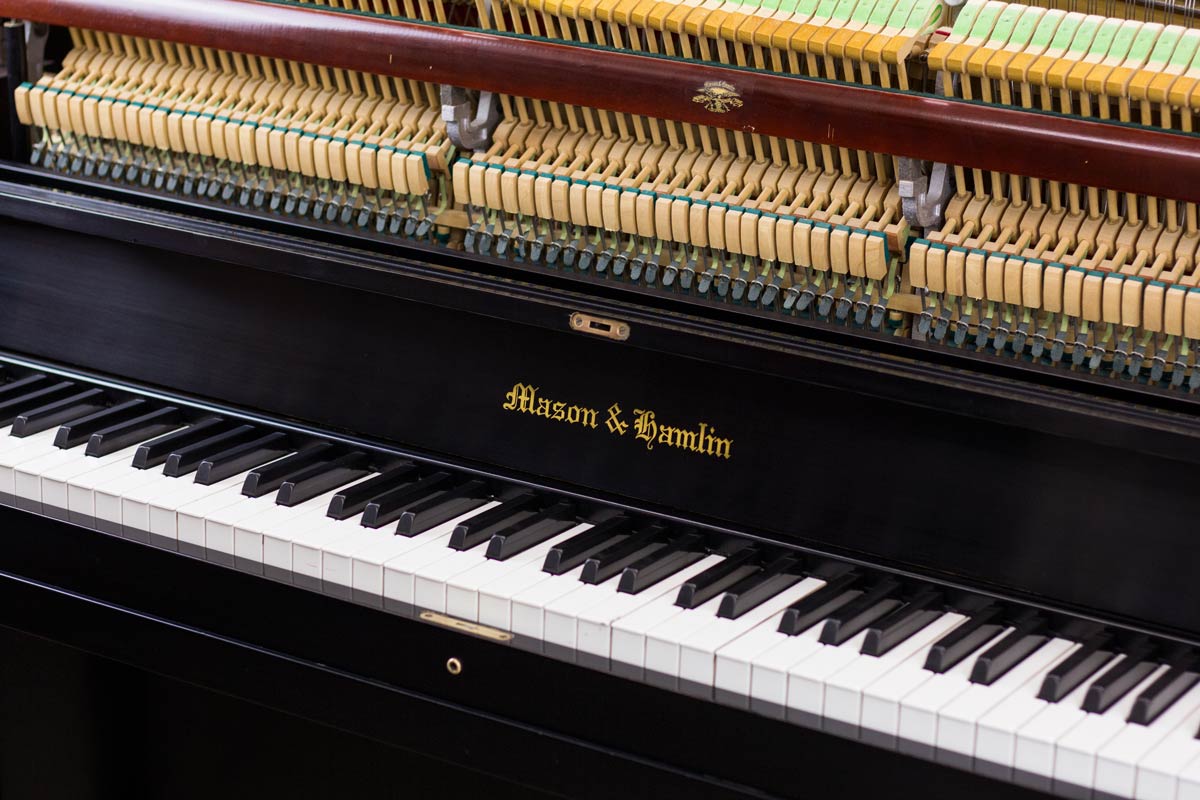
MASON & HAMLIN PIANO COMPANY 35 Duncan Street Haverhill, Massachusetts 01830 91 Pianos made by: Mason & Hamlin Piano Co., Haverhill, Massachusetts. It was founded by Henry Mason and Emmons Hamlin with funds provided by Oliver Ditson and Henry's father, Lowell Mason. The company was renamed Mason & Hamlin Organ & Piano Co. The company was located on Cambridge St., then 277 Washington St., then 134 Tremont St., Boston, MA 1854-1888.

The bellows are working on their original cloth, however, and while they are holding reasonably well, it will be among the first restoration tasks I’ll complete.This is just about all the information that's survived the passing of time on the Mason & Hamlin Organ Co. The two Forte stops were disconnected for some reason, and once I reconnected them, they lifted both the front and back mutes as they should. Many of the felts and leather pieces are in good enough condition that I won’t have to replace them. I was impressed by the overall condition, the muting system, and the quality of the build. I will create a new back out of a suitable wood for the organ, as the current back is a piece of plywood held in by five impossibly undersized screws. Unfortunately the organ does not have its original back. There was a number hand-written behind the front fallboard, along with initials, presumably of the person who built it. I discovered that the organ had absolutely no markings, serial numbers, or anything immediately apparent labeling on the back or the inside. Over the weekend I was finally able to open the back of the Lindholm and inspect what is inside. After removing the treadles, the cabinet is now empty. Kitchen hinges!Īll the screws were different.
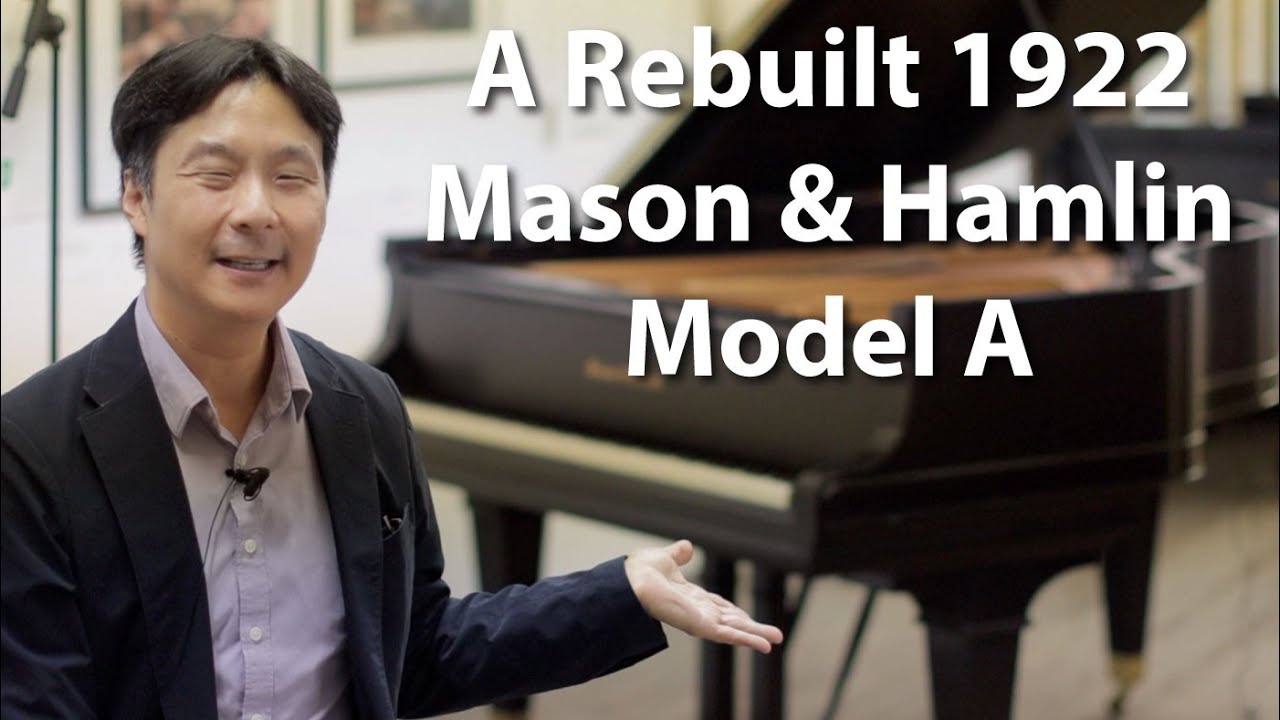
Someone created a kludgy “solution” to mounting the treadles. They had to use every bit of space on this organ! After removing the bellows from the organ, I remove the treadles. Instead of woven tape, they are made of wood:Īlso interesting is that the safety spill valve is mounted on the front of the reservoir and not on the back: The connectors to the treadles are really different. These are really tiny compared to what I’ve usually seen in an instrument, but that’s part of the fun of restoring a small instrument! After removing that, I move on to the bellows mechanism: the main reservoir and the exhausters. This must be fixed or the foundation board replaced. Taking a look at the foundation board, I notice that there is a huge crack: Here’s another look at the cleaned up reed pan. The repairs to the cracks are not perfect but hopefully it will be good enough. I’m hoping that it will improve the “soundboard” qualities of the reed pan. It is supposed to have greater elastic properties that allow the wood to move with the vibrations created by the reeds. We will see whether the violin varnish is an improvement over regular shellac. Actually, instead of shellac, I used a special type of violin varnish, whose primary component is shellac. Once the sanding was finished, I applied the first coat of shellac. I sanded the entire reed pan, reset all of the joints, glued and clamped around all sides.Īfter I made the repairs, the reed pan joints are now tight and square. The reed pan had also warped and was partially coming apart. All of the screws were heavily corroded and were cleaned up by using a rotating wire brush. I patched the cracks, cutting a v-groove with a file and splicing in some new hardwood. It had a lot of moisture damage, with mold and dis-coloration everywhere, in addition to several cracks. The reed pan was in worse shape than I expected.
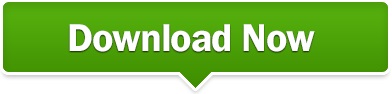